Особенности и методы испытаний арматуры газо- и нефтепроводов на огнестойкость
Повышение пожарной безопасности объектов нефтегазохимического комплекса входит в число важнейших задач по защите населения и окружающей среды от угроз техногенного характера. Горение углеводородов протекает по собственному сценарию, отличному от стандартного. Типовые средства огнезащиты в этой ситуации неэффективны, поэтому пожары и взрывы на нефтяных платформах, газовых установках, перерабатывающих заводах почти всегда сопровождаются человеческими жертвами и весомым материальным ущербом.
Для того чтобы противостоять огню, конструкции, узлы и элементы газо- и нефтепроводов должны обладать повышенной устойчивостью. Подтверждают ее в особых лабораторных условиях. Рассмотрим подробнее, в чем заключаются особенности углеводородного горения и как проходит испытание арматуры на огнестойкость.
Режимы углеводородного горения при испытаниях на огнестойкость
Стандартным режимом, при котором проводят испытания на огнестойкость и который максимально приближен к температурному режиму обычного пожара, является так называемый целлюлозный режим. С точки зрения температурного воздействия этот вариант можно отнести к категории «лайт». Условия такого горения определяет ГОСТ 30247.0-94 «Конструкции строительные. Методы испытаний на огнестойкость. Общие требования», согласно которому зависимость температуры от времени в условиях пожара описывается уравнением: T – Т 0 = 345 х lg (8t + 1), °С. Испытания в данном режиме обычно актуальны для элементов инженерных систем на таких объектах инфраструктуры, как вокзалы, аэропорты, торговые центры, стадионы… Согласно расчетным величинам в течение 5 минут температура достигает 580 °С, в течение 1 часа — 950 °С (см. рис. 1).
Рис. 1 . График зависимости температуры в огневой печи от времени нагрева для целлюлозного и углеводородного температурных режимов (ГОСТ Р ЕН 1363-2-2014)
При этом для углеводородов (нефть, нефтепродукты, природный газ) присущ абсолютно другой механизм горения. Уже в первые 5 минут после возгорания температура приближается к отметке в 948 °С, стремительно нарастая. В связи с этим углеводородное горение выделено в отдельный класс. Его описывают американский стандарт ANSI / UL 1709 и отечественный ГОСТ Р ЕН 1363-2-2014 «Конструкции строительные. Испытания на огнестойкость. Альтернативные и дополнительные методы». Кроме того, на объектах нефтегазовой отрасли значительная часть оборудования находится под давлением. Разрушение конструкций с выходом наружу горючего вещества, в особенности газа, сопровождается возникновением свищей, реактивных струй и факельного воспламенения. Это влечет за собой масштабные разрушения, значительный материальный ущерб и риск большого числа человеческих жертв.
Для буровых платформ, нефтеперерабатывающих заводов, газопроводов и других объектов, напрямую взаимодействующих с углеводородами, должны применяться специальные огнезащитные средства и составы, испытанные в условиях углеводородного горения.
Стандарт ГОСТ Р ЕН 1363-2-2014 закрепляет необходимость испытаний отдельных объектов и элементов инженерных систем на огнестойкость не только при стандартном, но и при альтернативных режимах. В частности, при огневых испытаниях арматуры для газо- и нефтепроводов и других конструкций, применяемых в нефтяной промышленности, создают более жесткие условия. В углеводородном режиме температура и давление возрастают гораздо быстрее и имеют б?льшие значения, чем при горении древесины и других строительных и облицовочных материалов. Его используют при определении предела огнестойкости строительных конструкций, применяемых на объектах нефтяной промышленности, но не только…
Методы испытаний трубопроводной арматуры на огнестойкость
Трубопроводная арматура — это система деталей, крепежных узлов и приспособлений, установленных на трубопроводах и агрегатах для регулирования потока рабочей среды (жидкости, газа). Она включает в себя следующие элементы:
- задвижки;
- клапаны;
- вентили;
- заслонки;
- конденсатоотводчики;
- краны;
- регуляторы давления, расхода и уровня.
Вид арматуры зависит от назначения:
- Запорная — герметично перекрывает или открывает поток в трубопроводе. Это краны, вентили, клапаны, задвижки, заслонки, затворы.
- Регулирующая — изменяет уровень и давление рабочей среды в трубопроводе. Это регулирующий клапан, регулятор давления и уровня, смесительный клапан, регулирующая заслонка и задвижка.
- Защитная — защищает трубопровод и оборудование от аварийного изменения параметров или изменения потоков, отключает аварийный участок. Это обратный клапан и обратный затвор, отключающий отсечный клапан, задвижка с пневматическим приводом и т.д.
- Предохранительная — защищает от повышения давления выше нормативного значения. Это предохранительный клапан, импульсное предохранительное устройство, перепускной клапан и т.д.
- Распределительно-смесительная — распределяет потоки рабочей среды по указанным направлениям или смешивает их. Это распределительные краны, клапаны, трехходовая арматура.
Общие требования к безопасности элементов определяет ГОСТ 12.2.063-2015 «Арматура трубопроводная. Общие требования безопасности». В пункте 4.3 документа подробно прописаны условия, соблюдение которых обеспечивает безопасную эксплуатацию арматуры. Вот некоторые из них:
- Материалы для основных деталей арматуры должны быть выбраны с учетом условий эксплуатации и опасности рабочей среды. Для взрывоопасной среды используют искробезопасные, для пожароопасной — огнестойкие материалы.
- Арматура должна обладать запасом прочности, быть устойчивой к перепадам давления, температуры, коррозии, сейсмической активности и иным внешним воздействиям.
- Термическая безопасность арматуры при температуре рабочей среды выше 50 °C или ниже минус 40 °C должна обеспечиваться термоизоляцией, установкой ограждений, конструктивным исполнением.
- Сборку и монтаж необходимо проводить в соответствии с регламентируемыми процедурами.
- Прочность и плотность материалов, сварных швов и соединений необходимо подтверждать испытаниями, в том числе на огнестойкость.
Испытания арматуры в режиме углеводородного горения относятся к категории специальных. Это определено «ГОСТ 33257-2015. Арматура трубопроводная. Методы контроля и испытаний». Согласно нормативно-техническому документу, специальные испытания проводят для подтверждения стойкости арматуры к климатическим, механическим и термическим воздействиям (на огнестойкость). Необходимость и объем таких испытаний определяют в зависимости от условий эксплуатации арматуры и ее назначения. Критерием оценки выступает подтверждение характеристик, указанных в конструкторской документации, при этом правила распространения результатов огневых испытаний, условия их использования в процессе приемки, отражаются в программе и методике испытаний арматуры.
При проведении испытаний могут учитываться требования других стандартов: ГОСТ 5761, ГОСТ 5762, ГОСТ 11823, ГОСТ 12893, ГОСТ 13252, ГОСТ 13547, ГОСТ 21345, ГОСТ 24570, ГОСТ 28343, ГОСТ 31294. Но основным для проведения огневых испытаний является национальный стандарт ГОСТ Р ЕН 1363-2-2014. Общие требования к проведению испытаний на огнестойкость в условиях пожара установлены руководящим документом СТ ЦКБА 001-2003. Здесь же установлен основной метод испытаний трубопроводной арматуры на огнестойкость. Сущность метода — в определении времени от начала теплового воздействия на испытуемую арматуру (далее — ИА) до наступления одного или нескольких предельных состояний огнестойкости:
- потеря герметичности затвора (утечки, превышающие нормы по ТУ), сальникового уплотнения и уплотнения корпус-крышка;
- потеря способности изменять положение и перемещаться из положения «открыто» в «закрыто» и наоборот;
- изменение параметров регулирования (для регулирующих клапанов);
- нарушение геометрических форм и размеров деталей, появление трещин, прогаров и прочих дефектов, препятствующих нормальной работе.
Испытания арматуры трубопроводов на огнестойкость проводят:
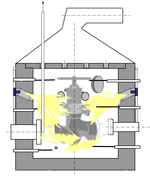
- в ее заполненном водой состоянии;
- под давлением в соответствии с методикой испытаний;
- в условиях рабочей среды, установленных в руководящем документе;
- в закрытом горизонтальном положении;
- при воздействии пламени с температурой от 750 до 1000 °С;
- до наступления предельного состояния.
Далее производят регистрацию одного или последовательно нескольких предельных состояний по огнестойкости. После охлаждения дополнительно проводят гидравлическое испытание арматуры с целью проверки герметичности узлов.
Оценка средств огнезащиты в режиме углеводородного горения
Огнезащита представляет собой комплекс конструктивных или технологических приемов, которые позволяют снизить пожарную опасность. Огнезащита призвана решать две глобальные задачи: предохранять конструкции от разрушения до приезда пожарной бригады и дать время для эвакуации людей. При использовании средств огнезащиты крайне важно учитывать тип горения, которое может возникнуть на конкретном объекте. Так, средства, разработанные для целлюлозного горения, при углеводородном пожаре окажутся неэффективными. Причиной тому — принципиально иной характер развития пожара.
Как уже отмечалось выше, для горения углеводородов характерен стремительный рост температуры до отметок, значительно превышающих стандартные, — до 1000 °С за первые 5 минут пожара. На огнезащитное покрытие обрушивается удар волны пламени, происходит рост давления. В связи с этим для действенной и надежной защиты необходимы особые физико-химические свойства защитных составов. При обеспечении пожарной безопасности нефтегазовых объектов следует ориентироваться на наиболее жесткие и драматичные ситуации, которые могут возникнуть в ходе пожара.
Основной метод испытаний установлен в американском стандарте ANSI / UL 1709 «Оценка стойкости покрытия конструкционной стали в условиях стремительного роста температуры». Стандарт определяет критерии стойкости огнезащиты при углеводородном горении. Испытания проводят в условиях температуры, приближенной к 1000 °С. Кроме тепловой нагрузки, материал должен обладать устойчивостью к веществам и средам, характерным для углеводородного горения.
Средства огнезащиты не подлежат обязательной оценке при углеводородном горении. Однако проведение испытаний может потребоваться при добровольной сертификации, а также для оценки соответствия требованиям проектной документации.
В рамках испытаний, как правило, проводят оценку:
- огнезащитной эффективности средств;
- толщины огнезащитного покрытия;
- наименования средства и его срока службы;
- вида, марки и толщины, контактирующих со слоем огнезащиты грунтовых, атмосферных или декоративных покрытий.
Углеводородное горение может возникнуть не только на объектах нефтехимической и газовой отрасли, но и в гражданском строительстве, например на газовых линиях. Поэтому в мировой практике при строительстве многоэтажных зданий и сооружений особой важности (например деловые центры Лондона и Нью-Йорка) приоритет отдан покрытиям, которые выдерживают условия углеводородного пожара.
Этапы проведения испытаний
Испытание арматуры нефте- и газопровода, также как и огнезащитных покрытий, проходит в несколько этапов. Заказчик направляет заявку в испытательную лабораторию и вместе с ней предоставляет:
Для арматуры:
- сборочный чертеж изделия;
- техническую документацию;
- паспорт изделия;
- программу и методику испытаний на конкретное изделие, разработанные на основании СТ ЦКБА 001-2003 и требований заказчика (при наличии).
Для средств огнезащиты:
- техническую документацию (ТУ, описание и т.д.);
- инструкцию по нанесению;
- программу и методику испытаний (при наличии).
Заказчик заключает договор с лабораторией. В документе прописываются в том числе и сроки проведения работ.
Следующий этап — отбор образцов и, непосредственно, сами испытания. Проводить их допустимо только на аттестованном оборудовании, специальном стенде.
В качестве образцов, на которые наносится (монтируется) средство огнезащиты, должны использоваться стальные колонны двутаврового сечения профиля № 20 по ГОСТ 8239 или профиля № 20Б1 по ГОСТ 26020. Высота образца (1700 ± 10) мм. Приведенная толщина металла стальной колонны определяется непосредственно перед каждым испытанием. Также допускается проведение испытаний на других видах профиля.
Средство огнезащиты наносится (монтируется) на образцы в соответствии с технической документацией (зачистка поверхности стальных образцов, тип грунтовки, количество и толщина наносимого слоя и т.д.).
В ходе подготовки к испытанию запорной и других видов арматуры образец необходимо разместить в огневой камере и подключить к переходным трубопроводам для создания внутри задвижки необходимого давления
Температуру горения поддерживают в соответствии с уравнением углеводородного горения
T – T 0 = 1080 х (1 – 0.325 х e –0.167t – 0.675 х e –2.5t ).
Фиксировать значение требуется через каждые 60 секунд. В конце испытаний необходимо зарегистрировать время наступления предельного состояния ИА по огнестойкости.
Результаты оформляют в виде протокола. В нем содержатся следующие сведения:
- наименование испытательной лаборатории;
- наименование организации-заказчика;
- дата испытаний;
- рабочий чертеж ИА и его номер (для арматуры);
- указание нормативного документа на методы проведения испытаний;
- перечень параметров для контроля и результаты измерений;
- итог визуального наблюдения за испытанием;
- заключение об огнестойкости арматуры или огнезащитной эффективности состава.
Производитель (импортер) арматурных элементов или средств огнезащиты в случае успешных испытаний получает возможность беспрепятственно пройти добровольную сертификацию. Между тем испытания арматуры и средств огнезащиты в условиях углеводородного горения — процедура технологически сложная, требующая высокой точности испытательного оборудования и профессиональных знаний испытателя. Для того чтобы быть уверенным в достоверности результата, проводить испытания следует только в авторитетной аккредитованной лаборатории.